Decommissioning and removal of diesel storage tanks and associated pipework
Published 30 April 2025
Framing the challenge
A client in the water sector was undertaking a general revamp of their site, which involved multiple improvements to infrastructure. This required several redundant diesel storage tanks and chlorine storage tanks – including associated pipework and steel gantry sections – to be removed, posing significant engineering challenges.
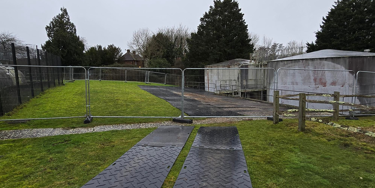
Following an initial site visit to assess the necessary works and prepare proposals, the team at our Tunbridge Wells depot took charge of the project. Given the potential impact to site operations, scheduling was of paramount importance, as the client required rapid completion with minimal disruption.
Approach and implementation
We proposed a comprehensive solution consisting of internal cleaning, decommissioning, demolition, and waste removal.
A specialist engineering team attended site to conduct an on-site risk assessment and mobilised plant and personnel to site. The tanks were then isolated and vented to ensure works could commence safely.
Cleaning
The first phase of works was to clean the tanks in preparation for demolition.
For the initial cleaning, we utilised a non-man entry solution, employing high-pressure water jetting, 3D rotating heads, and positioning booms. To complete the cleaning process and remove any final remnants, we undertook confined space man-entry cleaning, utilising task-specific PPE and line-fed breathing apparatus.
Following completion of the cleaning work, we collected and transferred the waste using our vacuum tanker fleet and disposed of it at a suitably licensed facility.
Demolition works
Given the complex and hazardous nature of the project, we used a range of equipment and processes to carry out the demolition works, including excavators, shears, and cold and hot cutting.
The demolition works on the two large diesel fuel tanks required working in confined spaces and using cold cutting to disassemble the tanks.
The chlorine tanks posed a real logistical challenge. These were situated inside a building and the limited access prevented the use of demolition machinery to deconstruct the tanks. To complicate matters further, the tank plate was double the thickness of standard vessels, therefore requiring an alternative method – in this instance, plasma cutters.
Due to the logistical and confined nature of the work, the cutting works presented additional hazards in the form of potential carbon monoxide and hydrosulphide gases. The on-site team had to work under full breathing apparatus with constant gas monitoring to prevent exposure to personnel at the workface, while also wearing appropriate in-visor welding masks due to the use of plasma cutting equipment.
The thickness of the tank shell combined with the logistical constraints meant that we had to carefully manage cutting of the tank to enable safe and efficient removal from the building.
Impact and outcomes
Our team managed several stakeholders throughout the project, including multiple safety and quality audits to ensure the works were progressing to plan.
Keeping the client informed at all stages through constant communication and daily situation reports as part of our overall turnkey process has been key to the success of this project.
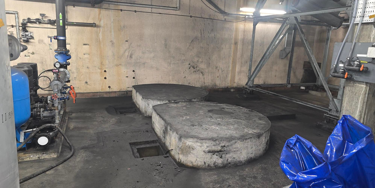
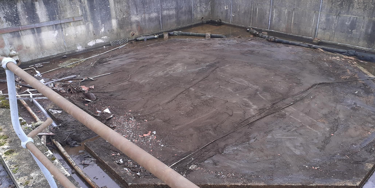
This structured approach ensured the project was completed safely, efficiently, and in accordance with all regulatory requirements, including the safe and compliant handling and disposal of all waste.
More from our Knowledge Hub
- case study
Decommissioning and removal of diesel storage tanks and associated pipework
- Insights
Earth Day 2025: Enabling a sustainable future while supporting today’s infrastructure in an evolving energy landscape
- Insights
Mitigating climate change risks through planned preventive maintenance
- Insights
Protective coatings: Safeguarding infrastructure against climate change
Environmental compliance today, creating a sustainable tomorrow
Helping you reduce risk to the environment and your operation by managing assets compliantly while achieving commercial, ESG, and net-zero goals.
Contact our experts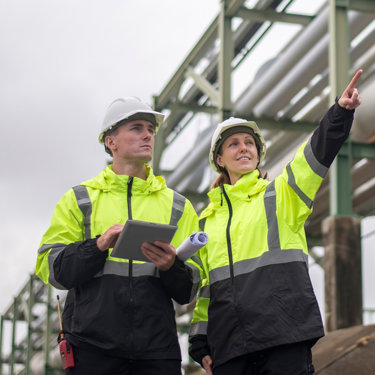