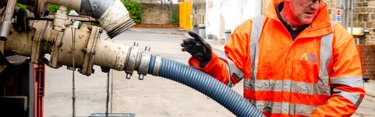
Oil-water separator services
Ready to discuss your project?
Please leave your details and a member of our team will reach out to discuss your requirements in more detail and arrange next steps.
We help operators of sites with oil storage remain compliant with current legislation so that you can reduce the risk of an environmental incident, regulatory fines, operational downtime, and reputation damage, by specifying, installing, inspecting, maintaining and remediating your separators.
A separator (or interceptor) is a trap installed to surface water drainage to protect the environment from petrol, diesel, oil and silt pollution.
Also known as tertiary containment, separators minimise the consequences of a major incident that causes the failure of or exceeds the storage capacity of secondary containment and enables additional measures to be deployed in time if an incident escalates.
A separator is required for car parks which are over 800 sqm (which equates to 50 or more parking spaces), roads, vehicle maintenance facilities, petrol stations and other refuelling sites, or industrial sites that have oil storage.
Benefits
- Remain compliant with BS EN 858-1:2002, 2:2003 and GPP3.
- Specify, install, commission, inspect, test, and maintain your separators compliantly.
- Receive a full report following any inspections.
- Manage disposal of hazardous waste.
Added value
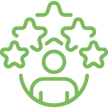
In-house experts
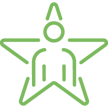
Capability
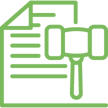
Compliance
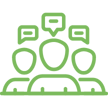
Consultancy
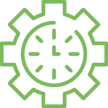
Extend asset lifespan
Key stats
- 0We have maintained 5,000 separators across the UK.
- 0+150+ current separator contracts.
Specification and installation
The current standard by which separators should be designed and tested is BS EN 858-1:2002 Separator systems for light liquids (e.g. oil and petrol) - Principles of product design, performance and testing, marking and quality control.
GPP3: Use and Design of Separators In Surface Water Drainage Systems is based on BS EN 858-1:2002 and states:
- Where separators are needed
- How to choose the right type of separator
- The different types of separators
- Maintenance and use
- Incident response
Use the flow chart to help you select the appropriate system for your site. Insert GPP flow diagram.
Consider the local circumstances and risk factors including:
- the discharge point of your proposed separator.
- the environmental sensitivity of your location.
- activities on your site.
Maintenance
The current standard by which separators should be operated and maintained, is BS EN 858-2:2003 Separator systems for light liquids (e.g. oil and petrol), it states separators should:
- Be fitted with an automatic warning device/high level alarm.
- Be serviced and maintained as a minimum on a 6 monthly basis.
- Be subject to a maximum interval of a 5 yearly integrity test.
- Have full service and maintenance records available for inspection.
Determining regulatory action
A pollution incident as a result of a poorly maintained asset such as a separator is a strict liability offence.
The two laws the regulators would be looking to establish that you had breached in the event of an environmental incident are:
The Water Resources Act 1991 (as amended)
It is an offence to cause or knowingly permit any poisonous, noxious or polluting material, or any solid waste to enter any controlled water.
Environmental Permitting Regulations 2016
It is an offence to cause or knowingly permit a water discharge activity or a groundwater activity without an environmental permit (regulation 38, EP Regulations 2016).
Which separator is right for my site?
Separators are split into class 1 and class 2 and can be full retention or bypass.
Class 1 separator
- Designed to achieve a discharge concentration of less than 5mg/ltr of oil in the discharge.
- Class 1 allows discharge to surface or foul water drainage.
- Class 1 separator will have a coalescing filter present.
Class 2 separator
- Designed to achieve a discharge concentration of less than 100mg/ltr of oil in the discharge.
- Class 2 can only allow discharge to foul sewer.
By-pass
Description: Treat all flows generated by rainfall rates of up to 6.5mm/hr. These separators are used when it is considered an acceptable risk not to provide full treatment for high flows, for example where only small spillages occur and the risk of spillage is small.
Application areas: Car parks / roadways & major roads / light industrial & goods yard.
Full retention
Description: Treat the full flow that can be delivered by a drainage system. Full retention separators are used where there is a risk of regular contamination with oil and a foreseeable risk of significant spillages eg) vehicle maintenance areas.
Application areas: Sites with high risk of contamination / fuel storage depots / refuelling facilities / vehicle maintenance areas or workshops
Environmental compliance today, creating a sustainable tomorrow
Helping you reduce risk to the environment and your operation by managing assets compliantly while achieving commercial, ESG, and net-zero goals.
Contact our experts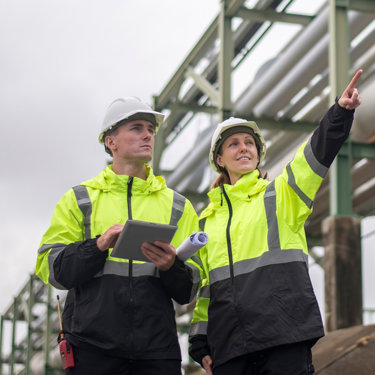