Quick Guide: BS EN 858-2:2003
Published: 29 March 2023 | Download Quick Guide
This Quick Guide looks at BS EN 858-2:2003, the legal implications, why it's important to act, and what you should do to apply this standard to your organisation.
Summary
BS EN 858-2:2003 (Separator systems for light liquids e.g. oil and petrol) is the national standard introduced by EU members in 2002 and fully adopted by BSI in 2003, and provides guidance on the specification, installation, operation, and maintenance of light liquid separators.
Separators (also known as interceptors) are installed on sites that treat potentially oil contaminated rainwater (run-off) from impervious areas, and to hold any spillage of light liquids to protect controlled waters (any surface waters leading to foul drains, ground water, rivers/streams etc) from possible hydrocarbon pollutions.
The guidance establishes the size, type and class of separator needed to protect a drainage catchment area and is based on a number of variables and provides an agreed formula for businesses to calculate.
Variables might include the activities taking place in the drain area (e.g. refuelling), the size of the area drained, and where it is discharging to (storm water overflows or to sewers).
The legal perspective
There is a range of legislation issued by the different regulatory bodies in the UK that provides the legal viewpoint on pollution events caused by poorly maintained or wrongly specified separators, or separators not installed:
- The Environmental Permitting (England and Wales) Regulations 2016, and The Pollution Prevention and Control (Scotland) Regulations 2012
- The Water Environment (Oil Storage) (Scotland) Regulations 2006, and the Control of Pollution (Oil Storage) (Amendment) Regulations (Northern Ireland) 2011
- Pollution Prevention and Control Act 1999
This legislation, along with others, is then supported by the additional BS EN 858-2:2003 standard and GPP 3 guidance to help businesses to be able to act accordingly and establish correct procedures for separator installation and ongoing maintenance.
Standards and good practice are designed to assist an operator to understand what the law requires, and how to comply with it.
Businesses must follow the appropriate legislation, standards, and good practice to ensure that they are doing everything reasonably practicable to ensure risks in relation to pollution spills are reduced.
Should an unfortunate spillage occur, then the environmental regulator will be looking at where legislation hasn’t been followed but will also be examining if guidance and good practice has been implemented to aid in a safe and secure operation.
Why you must act
Following the good practice set out in BS EN 858-2:2003 helps companies to massively reduce the pollution risks associated with their operations, specifically in relation to hydrocarbon pollution incident from the structured drainage system.
In addition to this, there are further elements that can be avoided with adoption of the guidance.
Penalties and reputational issues
Separator units that are incorrectly specified, installed, and not regularly maintained can result in pollutants escaping and causing environmental harm.
Huge fines have been imposed on companies that have experienced a pollution event and these fines have increased significantly where they haven’t applied the guidance laid out in BS EN 858-2:2003.
In addition to the operational impact of downtime to ensure clean-up of the pollution, and the financial impact of fines, there is also a negative effect on the company’s reputation. Businesses endeavour to improve their reputation and their image of being a safe operator, and both are significantly impacted when they experience a pollution event.
A pollution event due to an wrongly specified or poorly maintained separator could invalidate a businesses’ insurance cover.
Practical application
The guidance is very specific in relation to the maintenance of separators.
They should:
- Be fitted with automatic warning devices
- Be serviced and maintained as a minimum on a six monthly basis (in service)
- Be subject to a maximum interval of 5-yearly integrity test (out of service)
- Have up to date, and available on request, cleaning and maintenance records
All cleaning and maintenance records should be kept and made available to the authorities upon request and should contain remarks on specific events (e.g. repairs, accidents).
Ensuring that separators are regularly checked and maintained is essential in proving to the regulatory bodies that you have reduced risk and consequences of pollution incident caused by either a spill or a slow leak over time.
An environmental partner can guide you through this process, ensuring records are maintained and stored, and providing remedial works to separators if required.
What you should do
- Ensure all separators are installed correctly and maintained as specified in the standard.
- Ensure the appropriate maintenance records for separators are available to present to regulators.
- Ensure regular checks are made on your separators, so if a pollution event occurs, it can be identified and resolved as soon as possible.
- Work with an environmental partner who can guide you through the required inspection and maintenance regimes to ensure your sites remain compliant.
You can find all our Quick Guide downloads here.
Environmental compliance today, creating a sustainable tomorrow
Helping you reduce risk to the environment and your operation by managing assets compliantly while achieving commercial, ESG, and net-zero goals.
Contact our experts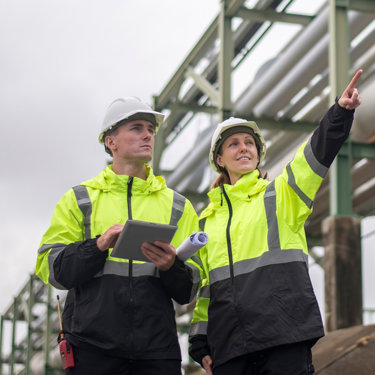