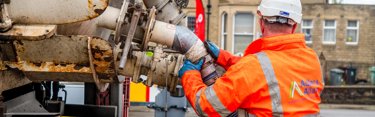
Planned preventive maintenance
Ready to discuss your project?
Please leave your details and a member of our team will reach out to discuss your requirements in more detail and arrange next steps.
We help organisations ensure their assets remain compliant by establishing a planned preventive maintenance (PPM) regime so that you can extend the lifespan of your assets and ensure you have up-to-date inspection and maintenance documentation available on request in the event of a pollution incident.
A planned preventive maintenance contract means that maintenance tasks are scheduled to take place regularly, and then documented to provide proof of diligence in the event of an incident.
The idea is to prevent problems before they occur and reduce the long-term cost of the asset.
Reactive maintenance can solve the problem in the short term, but it makes financial planning difficult, often has higher asset lifecycle costs, and could attract more robust regulatory enforcement action and cause more damage and injury in the event of an incident.
Planned preventive maintenance reduces the overall cost of ownership, helps maintain compliance with relevant standards and good practice guidance. It can also extend asset lifespan, increase safety on site, reduce downtime and the likelihood of environmental damage and negative publicity.
Features and outputs
- In most instances assets can remain operational while maintenance takes place.
- Work is planned in so you can manage your budget and you don’t need to remember when your next inspection is due.
- A correctly documented PPM schedule can help partners demonstrate they have taken all reasonably practicable measures to mitigate the risk of a pollution incident.
- A correctly managed asset greatly reduces your environmental risk.
- Our in-house team of experts can manage any remediation work identified as part of your routine maintenance contract.
We supply you with the appropriate PPM schedule and all relevant documentation demonstrating that equipment is maintained in line with manufacturer’s instructions, industry agreed good practice, and relevant standards.
We specialise in PPM contracts for:
- Tank inspections
- Tank maintenance
- Drains and drainage networks
- Separators/Interceptors
- Forecourt maintenance link to forecourt sector page
- Septic tanks
- Guttering
- Macerators
- Pump stations
- Hazardous and specialist electricals
- Grease traps
Tank inspections
Our industry-leading experts will visit your site to assess your underground, ground level, or above ground systems.
Using the latest high-pressure or ultrasonic technology, our skilled engineers and specialist welders test for leaks and structural concerns, repair faulty tanks, and provide full follow-up documentation.
Our inspection and reporting services cover tanks used for fuel, water, chemical, and food storage, and are compliant with EEMUA Level 2, API, OFTEC and NDT standards.
Tank cleaning and maintenance
We clean and purge all types of storage tanks in a variety of sectors, from retail forecourts, transport, major refineries, and military estates with underground, ground-level, or above-ground systems.
We employ man-entry and non-man-entry techniques to remove and dispose of any condensation, water, or sludge in your tank.
Manual and automated cleaning options are available, including powerful remote-controlled mechanical washers that comply with current legislation for oil, alternative fuel, and foul tanks, and storage containers for chemicals, water, and any other liquid or gas.
Separator maintenance
We help site operators that use, store, process, or re-fuel light liquids to remain compliant with current legislation, standards, and good practice, by inspecting, maintaining, and repairing your separators and alarms. This can significantly reduce the risk of an environmental incident, regulatory fines, operational downtime, and reputation damage.
Our experts will ensure you have full-service records in line with BS EN 858-2:2003, compliant with all inspection and audit requirements.
Drains and drainage networks
Through our Group companies Jet Aire and Oneline we help commercial drainage infrastructure owners and domestic customers with our reactive and proactive maintenance to keep their network flowing smoothly, improve efficiency, and manage environmental risk.
Hazardous and specialist electrical
Throughout your hazardous and specialist electrical equipment’s lifecycle we can maintain it in accordance DSEAR legislation, safeguarding the health and safety of your workers and your operational continuity.
We have in-house CompEx electrical engineers, with a detailed knowledge of both the current BS7671:18th edition and APEA requirements for the maintenance of filling stations.
You might also be interested in...
Environmental compliance today, creating a sustainable tomorrow
Helping you reduce risk to the environment and your operation by managing assets compliantly while achieving commercial, ESG, and net-zero goals.
Contact our experts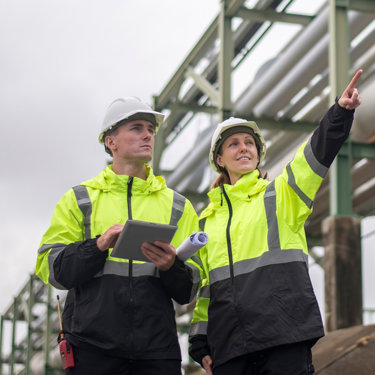