Mitigating climate change risks through planned preventive maintenance
Published: 10 April 2025
Climate change poses significant risks to businesses, particularly those with extensive site infrastructure and assets. Extreme weather events, rising temperatures, and changing precipitation patterns can all impact the longevity and functionality of these assets. One effective strategy to mitigate these risks is the implementation of a planned preventive maintenance regime.
Planned preventive maintenance involves scheduling regular maintenance tasks to ensure assets remain in optimal condition. This proactive approach helps prevent problems before they occur, reducing the long-term cost of ownership and extending the lifespan of assets.
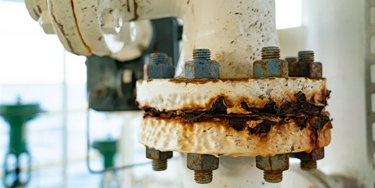
Predictive maintenance for cost efficiency
Climate change introduces new financial risks for businesses, with extreme weather events becoming increasingly common in the UK. Regular maintenance can help businesses to mitigate the financial impacts of higher repair costs and increased downtime caused by significant damage to infrastructure.
Telemetry data is a powerful tool that can be used to assess the impact of climate-related events on industrial equipment. By understanding these impacts through real-time monitoring and analysis, site owners can implement preventive measures to protect their assets and ensure operational continuity.
Sensors placed in and around industrial sites can detect the presence of moisture or flooding and monitor water levels, providing real-time alerts when these rise above safe thresholds. This can help site owners to identify areas prone to flooding and assess the extent of water damage to equipment, aiding the planning of effective drainage solutions and protective barriers.
Temperature sensors can be used to monitor the ambient and operational temperatures of industrial equipment. The data from these sensors can be used to track temperature fluctuations and identify instances of overheating or freezing. Understanding these temperature variations can help site owners determine the impact of extreme heat or cold on equipment performance and lifespan. Preventive measures, such as installing insulation or cooling systems, can be implemented based on this data.
Telemetry systems can monitor wind speeds, atmospheric pressure, and other storm-related parameters. Sensors can also detect structural vibrations and stress caused by high winds. Analysing telemetry data allows site owners to assess the structural integrity of buildings and equipment during storms. This information is crucial for reinforcing vulnerable structures and ensuring the safety of personnel.
Extending asset lifespan with protective coatings
Climate change can accelerate the degradation of infrastructure.
Protective coatings are a vital component of a comprehensive maintenance strategy aimed at extending the lifespan of industrial assets. Regular maintenance, combined with the strategic use of protective coatings, ensures that equipment operates efficiently and lasts longer, ultimately providing better return on investment.
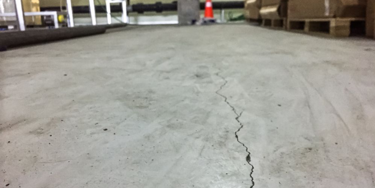
Using protective coatings as a barrier against moisture, chemicals, and other corrosive elements is particularly important for metal structures such as storage tanks and equipment exposed to increasingly harsh environmental conditions caused by climate change. By preventing corrosion, these coatings help maintain the structural integrity of assets, reducing the need for frequent repairs and replacements.
Applying a waterproof coating as a roof lining significantly enhances lifespan and protects the premises and the assets within from damage caused by heavy rain, snow, and extreme temperatures. Waterproof coatings can also be applied to walls, floors and structures to ensure impermeability, safeguarding them from the devastating impacts of flooding.
Managing increased rainfall and flooding with drainage maintenance
The increased frequency and intensity of extreme rainfall events caused by climate change can overwhelm drainage systems, leading to flooding and water damage.
Debris such as leaves, sediment and litter can accumulate in drainage channels, pipes and culverts, leading to reduced capacity and potential blockages. These blockages can cause water to back up, resulting in localised flooding and damage to infrastructure.
While routine inspections and cleaning can help prevent debris build-up, it may be necessary to upgrade existing drainage infrastructure to increase the capacity of drainage channels in response to changing climate conditions.
Poorly maintained drainage networks can result in floodwater inundating industrial facilities, causing extensive damage to structures, machinery, and stored materials. The force of the water can also erode foundations and compromise the integrity of buildings, while the resulting water damage can lead to cracks, shifts, or even collapse, necessitating costly repairs and potentially halting operations.
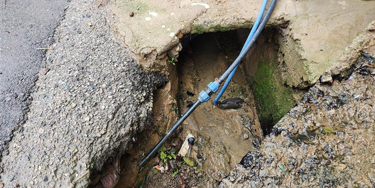
Site drainage can provide a primary pathway, so ensuring it is kept in good condition through regular inspections and maintenance is also key to mitigating the risk of a pollution incident that could be caused – or exacerbated by – climate change.
Protecting assets against extreme weather damage
Planned preventive maintenance is an essential proactive approach to protecting a wide range of industrial assets from the impacts of extreme weather conditions.
Maintaining gutters is crucial in preventing water damage to buildings. Gutters can easily become clogged with leaves, twigs, dirt, and other debris which can prevent water from flowing freely, causing it to overflow and spill down the sides of the building. Overflowing water can damage exterior walls, seep into foundations, and cause erosion around the building. Water can also back up onto the roof, leading to water damage and potential leaks. This can compromise the integrity of the roofing materials and lead to costly repairs.
Regular cleaning and inspections ensure that gutters can effectively channel rainwater away from the structure. Installing gutter guards can further reduce maintenance needs and improve water flow, protecting the building from leaks and foundation issues.
Regular maintenance of macerators is essential for preventing blockages and mechanical failures, ensuring efficient waste management even during extreme weather conditions.
Heavy rainfall and flooding can increase the volume of waste and water entering the macerator system. Proper maintenance ensures that the system can handle these increased loads without failing. Well-maintained macerators can efficiently process waste even during extreme weather events, reducing the risk of backups and contamination.
Climate change considerations
Planned preventive maintenance is not just about keeping equipment in good working order; it also has significant implications for regulatory compliance and risk management. Climate change introduces additional challenges for site and asset management. The increased frequency and severity of extreme weather events in the UK, such as storms, floods, and heatwaves, can significantly impact wear and tear on infrastructure.
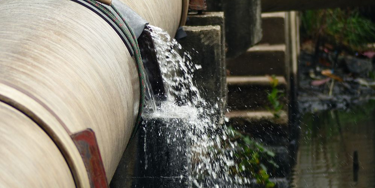
Many industries are subject to stringent regulations that mandate regular maintenance and inspections, and this can also contribute towards meeting key climate change regulations – particularly regarding energy use and carbon emissions. As climate change exacerbates wear and tear on infrastructure, compliance becomes even more critical.
Implementing a planned preventive maintenance regime is a proactive step that businesses can take to build resilience against climate-related impacts, while aligning with broader sustainability goals by reducing waste, conserving resources, and minimising the environmental footprint of operations.
We are committed to helping clients to navigate these challenges and secure a sustainable future through the provision of planned preventive maintenance contracts for a wide range of infrastructure and assets, including:
- Storage tanks
- Drains and drainage networks
- Separators/interceptors
- Septic tanks
- Guttering
- Macerators
- Pump stations
- Grease traps
More from our Knowledge Hub
- News
Adler & Allan awarded Gold in Defence Employer Recognition Scheme
- Case study
Decommissioning and redeveloping a mechanical transport fuel installation at Sennybridge Training Area
- News
Two prestigious wins at Water Industry Awards and Women in Utilities Awards 2025
- News
Celebrating and supporting our veterans at the Forces in Business Awards 2025
Environmental compliance today, creating a sustainable tomorrow
Helping you reduce risk to the environment and your operation by managing assets compliantly while achieving commercial, ESG, and net-zero goals.
Contact our experts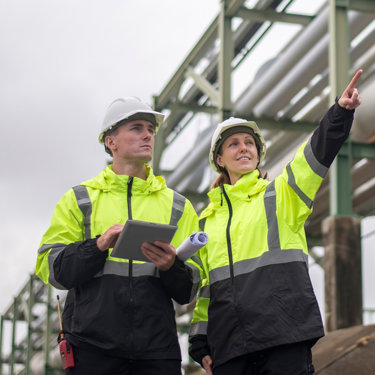