Safe removal of liquid anhydrous ammonia from bulk tank
Published: 27 August 2024
The problem
Due to a five-year statutory tank inspection and multiple system modifications, our specialist engineering team were called on to empty a tank of anhydrous ammonia and to purge the tank with dry nitrogen, removing all residuals and ensuring a safe working environment for the tank engineering contractor.
The ammonia supplier was unable to carry out this work due to the safety implications following the retirement of the technical manager at the logistics/tanker operator.
The solution
After arriving on site and following a documented debrief and induction with MAHLE, we set up a safe and secure working area, implementing a cordon to ensure no unauthorised access. All electrical equipment was isolated with a lockout-tagout (LOTO) system and additional earths as per the issued permit to work.
A toolbox talk and dynamic risk assessment were carried out to ensure all risks were mitigated to a safe level before work commenced. Site atmospheric detector devices were placed at designated zones to detect any hazardous elements during the decontamination process.
Due to the hazardous nature of the work, full chemical attire had to be worn at all times during the decontamination works. This was governed using the traffic light system to ensure the highest level of health and safety and assigning of correct personal protective equipment and respiratory protective equipment to personnel operating in each zone.
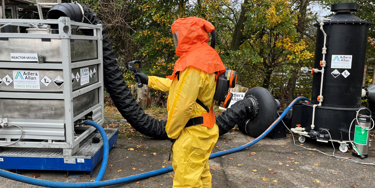
A mobile scrubbing unit, reactor vessel (sparging unit), UN-approved intermediate bulk container (IBC) storage bund and sulphuric acid solution (25%), nitrogen cylinder bank, and a chemical transfer pump were positioned within the cordoned zone. All equipment was earthed and continuity tested before operation commenced due to the hazards associated with the product. The static tank liquid valve feed was then connected to the reactor vessel with non-return valve and regulator, which in turn was connected to a pH probe and temperature gain to ensure a controlled reaction.
The mobile scrubbing unit extract hose was connected to the reactor vent, creating a closed-loop neutralisation process. The static gas valve was then slowly opened in a controlled manner and discharged into the reactor vessel. This was monitored until the desired neutralisation speed was reached, measured by pH, thermal reaction and vapour elevation until the IBC reached a pH of 6.
Spent liquid was then transferred via chemical transfer pump into a labelled, UN-approved IBC for disposal, and sulphuric acid solution replenished in the reactor vessel.
This process was repeated until the reactor vessel receiving pressure reduced. The nitrogen bank was connected to the vapour return line and the AST was charged to 5 bars to ensure all remaining ammonia heel was processed through the reactor.
Once the remaining liquid ammonia was neutralised, an AST was recharged with nitrogen to 5 bars, then discharged through the reactor vessel. The remaining ammonia levels were recorded through block-and-bleed configuration.
The tank was purged to a safe and complaint level, ensuring all risks had been mitigated for the contractor completing the tank testing & remedials.
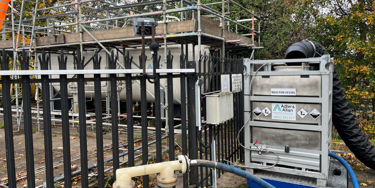
Project outcomes
We safely managed two concurrent reactions with coordinated involvement of our specialist engineering, SHEQ, and chemical advisory teams.
The site was safely demobilised, and all hazardous waste was removed via consignment note for compliant disposal.
MAHLE Engineering indicated how pleased they were with the operation and thanked us for the support provided. They also enquired about the provision of a 24/7 response service to ammonia release, as well as the supply-side of premium-grade ammonia and associated equipment in the event of a change of inputs from tanker to large drums.
More from our Knowledge Hub
- Insights
Mitigating climate change risks through planned preventive maintenance
- Insights
Protective coatings: Safeguarding infrastructure against climate change
- Insights
Delivering the Water (Special Measures) Act: Supporting compliance and innovation
- Insights
A guide to navigating climate change regulations for UK businesses
Environmental compliance today, creating a sustainable tomorrow
Helping you reduce risk to the environment and your operation by managing assets compliantly while achieving commercial, ESG, and net-zero goals.
Contact our experts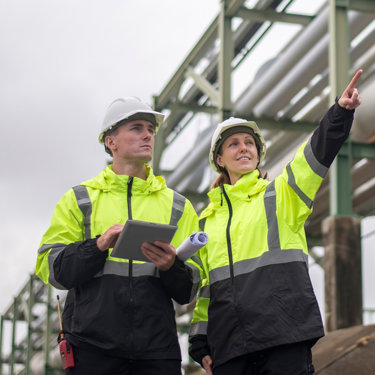