Installing polyurea coating for new transformer bund lining system at Bridgwater Substation
Published: 7 August 2024
The problem
We were asked to attend Bridgwater Substation to survey requirements for a bund lining solution within a transformer bund which was undergoing modifications. The modifications were uprating the existing bund to allow the installation of new equipment.
The scope of the project was to install a lining system within the bund, covering the base slab and containment walls to a level 300 mm above the highest plant support foundation. After installation, a 72-hour hydrostatic test was to be conducted in accordance with DNO standards to verify that full containment had been achieved.
Upon visiting site, we were presented with a concrete bund where the old transformer had been removed. With delivery dates scheduled for the new equipment, the area was ready to be handed over with the aim of completing the bund lining system as soon as physically possible.
The solution
We attended site and installed our polyurea coating to the area identified within the project scope. Polyurea is extremely fast setting, being tack-free in less than 10 seconds, allowing foot traffic almost immediately and use of the asset in less than 24 hours, which significantly reduces any downtime.
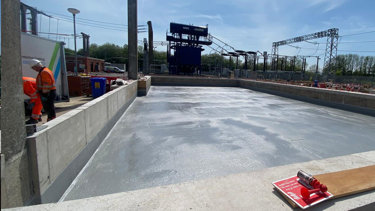
The fast-setting properties of polyurea, combined with its extraordinary tensile strength, abrasion resistance, waterproofing qualities and elongation of up to 400%, make it the ideal solution within this environment. It provides a strong, impermeable barrier that can expand and contract with the substrate to which it is applied without failure.
The team high-pressure jetted the area, removing all loose friable material as well as residual contamination. The waste uplift and extraction was managed by our fleet of tankers, removing the necessity for third-party involvement.
Once jetting works were complete, epoxy-based repair mortar and polyurethane sealant were used to repair areas where historic cracks or damage were apparent. Following this, a full coat of epoxy primer was applied to the area using brushes and rollers.
Once the specified height had been marked and masked, a 2000-micron coat of Polyurea was applied to the area using our integrated plural component proportioning system. Masking was then removed and finished edges were sealed with a neat bead of polyurethane sealant.
Once cured, a 72-hour water test was successfully carried out with zero failure rate in line with the DNO’s quality assurance standards.
Project outcomes
All works were completed on schedule, delivering a robust solution which will provide our client with a strong, impermeable barrier, ready for installation of the new equipment which was scheduled for imminent delivery. A quality solution delivered correctly and within schedule ensured our client remained on track with their overall project timeline and had confidence in the solution we were pleased to deliver.
More from our Knowledge Hub
- Case study
Decommissioning and redeveloping a mechanical transport fuel installation at Sennybridge Training Area
- News
Two prestigious wins at Water Industry Awards and Women in Utilities Awards 2025
- News
Celebrating and supporting our veterans at the Forces in Business Awards 2025
- Insights
Rebuilding trust in water: Interim recommendations from the Independent Water Commission
Environmental compliance today, creating a sustainable tomorrow
Helping you reduce risk to the environment and your operation by managing assets compliantly while achieving commercial, ESG, and net-zero goals.
Contact our experts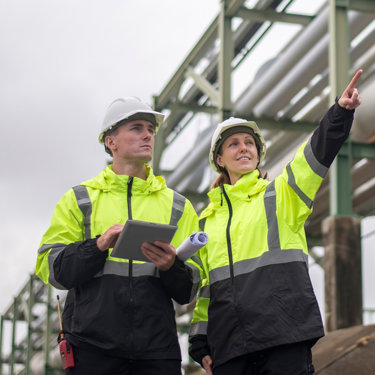