Beyond the blaze: Mitigation and innovative management of complex pollutants after major fire at Luton Airport car park
Published: 22 July 2024
The problem
On 10 October 2023, flames ripped through Luton Airport’s multistorey terminal 2 car park. The fire was declared a major incident, and more than 100 firefighters were deployed to bring the blaze under control.
Adler & Allan were called upon to help minimise the impact to the environment.
The solution
We arrived on site on day three of the incident to put in place a containment plan to minimise the impact of contaminants on the environment.
The first priority for the team was to isolate and contain contaminants and prevent these from entering the central soakaway. Key receptors, such as the interceptors that take the bulk of surface water run-off from the car park and wider site, were identified. Physical isolations were put in place which allowed the installation of over pump systems to control the flow of rainwater. This was a key priority as heavy rain on site was causing contamination run off from the incident location.
Environmental consultancy services were provided on this project undertaking soil, groundwater, and interceptor sampling to gain a full understanding of the incident and its impacts.
The ground investigation included rotary drilling of five locations approximately 70 metres into the chalk aquifer around the central soakaway to ascertain whether any contamination entered the groundwater.
Data analysis helped to identify the contaminants running off the site and to devise a solution. At a very early stage, it was established that this project would involve dealing with very high levels of hydrocarbon run-off.
Wear systems were installed to remove any free-phase product – anything floating on the water. The water was then passed through a Granular activated carbon (GAC) system to treat the dissolve-phase hydrocarbons. Through this system, the team were able to identify metals from electric vehicle batteries that posed a unique challenge.
To remove these metals, an ion exchange was employed using blend of selective resins to target the heavier metals and, over a period of eight weeks, this methodology was further refined.
We have also supported the demolition works in mitigating any environmental impact through the implementation of an environmental plan. This plan manages surface run-off, the safe removal of vehicles, all fuel-related products and ignition sources, and the construction of a bunded area location for onward transportation at a later date.
Project outcomes
- Approximately 1,300 cars involved in the fire incident introduced a unique volume of metal contaminants.
- A bespoke combination of wear systems, GAC and ion exchange employed to successfully treat wastewater.
- Over 11 million litres of contaminated water successfully managed, treated and disposed of.
- Environmental risks unique to the central soakaway successfully mitigated.
- Suppression systems – installation and maintenance.
- Ongoing assessment and monitoring to ensure environmental risks are successfully mitigated.
- Ongoing engagement with the Environment Agency to assist with the development of strategic guidance for the management of lithium batteries and associated incidents.
More from our Knowledge Hub
- Case study
Decommissioning and redeveloping a mechanical transport fuel installation at Sennybridge Training Area
- News
Two prestigious wins at Water Industry Awards and Women in Utilities Awards 2025
- News
Celebrating and supporting our veterans at the Forces in Business Awards 2025
- Insights
Rebuilding trust in water: Interim recommendations from the Independent Water Commission
Environmental compliance today, creating a sustainable tomorrow
Helping you reduce risk to the environment and your operation by managing assets compliantly while achieving commercial, ESG, and net-zero goals.
Contact our experts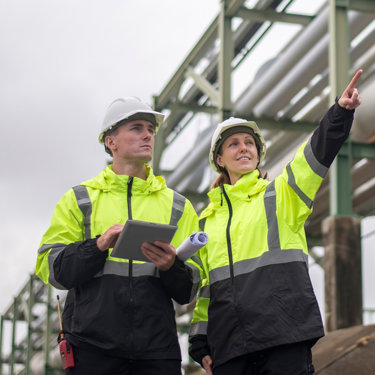